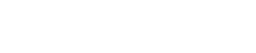
SMART SHIPPING
One more step towards operational intelligence
One more step towards operational intelligence
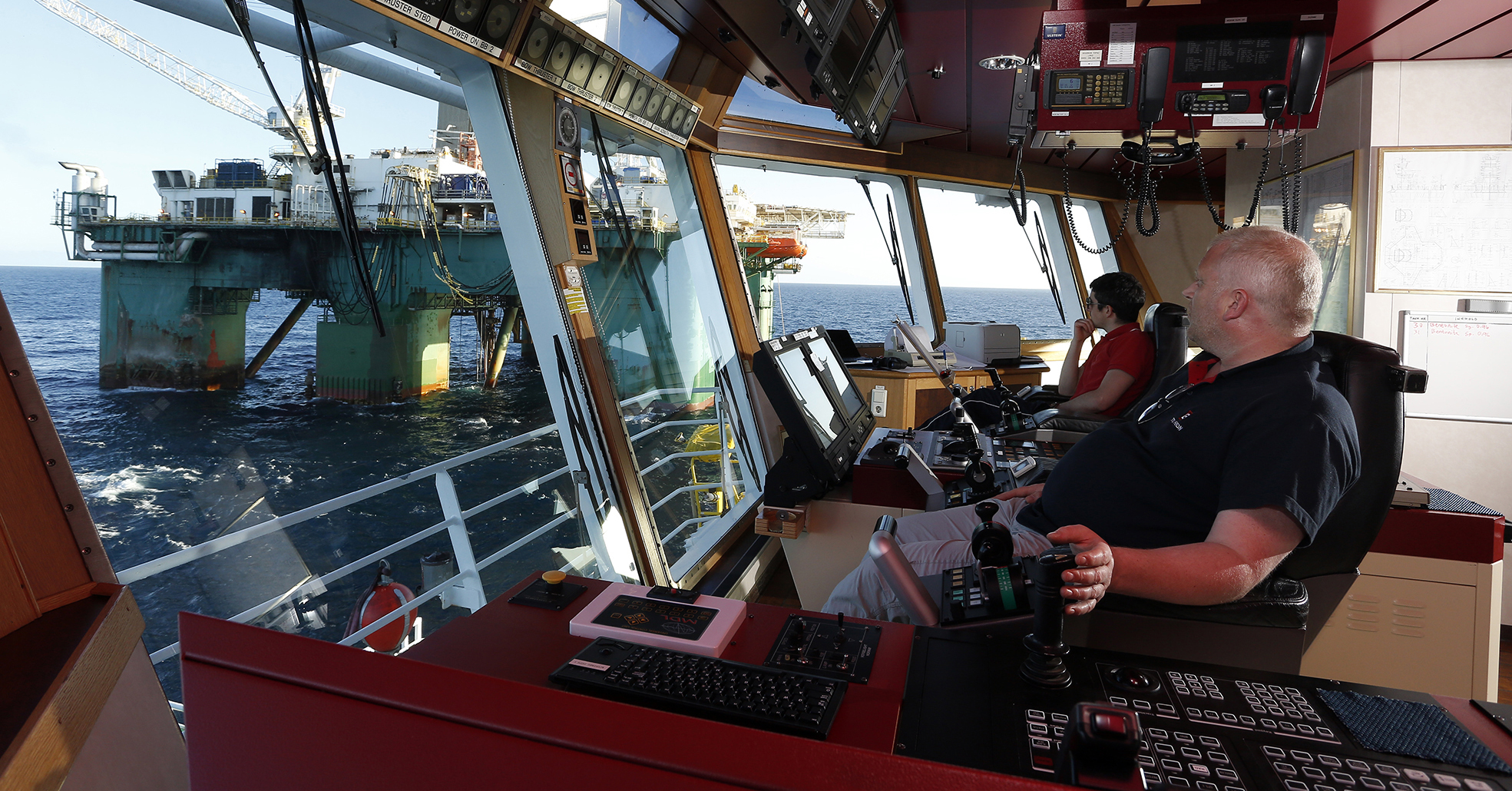
Toward a "Smart" Offshore
The severe crisis that offshore oil & gas is facing has rocked the entire industry and has accelerated changes to its different professions.
Faithful to its history, BOURBON, which constantly evolved over the past 20 years, has already made some strong decisions resulting in a transformation plan and a voluntary cost-reduction policy, highly necessary in this new economic context.
One illustration of this transformation, and the central topic of this magazine, is the Smart shipping program. It is aimed at ensuring safer, more efficient, and rationalized operations, thanks to innovations enabled by the digital revolution, for ever more operational excellence.
The Smart shipping program aims at ensuring safer, more efficient, and rationalized operations.
It's our turn to evolve, each and every one of us. The automation of onboard systems is already a reality for our seafarers and we must all innovate at speed to invent our business model and our professions of tomorrow.
The time has come for operational intelligence: connected vessels, the use of predictive maintenance, shore-based control centers, rationalization of tasks, etc.
The Offshore of tomorrow will be smart. Isn't it already?
Gaël Bodénès
Chief Executive Officer
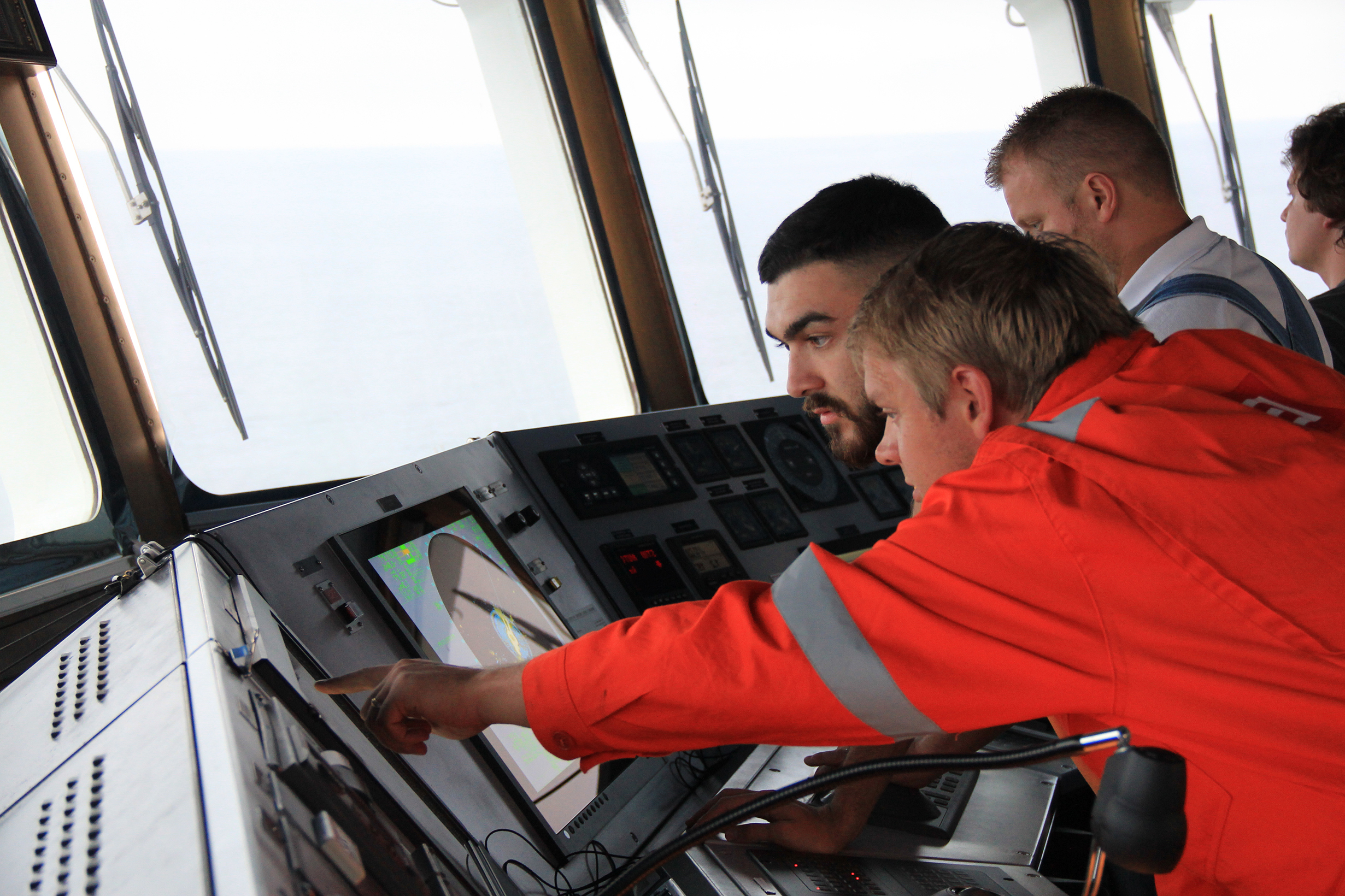
DP automation: a smart new system for greater safety
The new organization of the Dynamic Positioning, which combines smart technology with a change in organization, will mean greater safety for crews, as well as lower costs for BOURBON. BOURBON is now testing it on a contract for BP in Trinidad and Tobago. One more step towards operational intelligence.
Dynamic positioning
Core component of BOURBON strategy in Smart shipping, DP – Dynamic Positioning - is an automated heading and position control system. Whether it’s used to remain in position for a cargo operation or maintaining a heading and speed for a cable laying operation, the DP system has the ability to react at any moment to information transmitted by sensors regarding the impact of wind on the hull, draft or an external force generated by towing, a submarine cable being installed, or an underwater pipe during a pipe-laying operation. The system is operated by DP officers, who constantly monitor the system on the bridge and apply its recommendations.
Even though Officers are experienced and highly skilled, human error cannot always be avoided, whether a mechanical or computational mistake, or a moment of distraction or inattention. Bearing in mind that the cause of around 80% of collisions and near-misses in close proximity to offshore facilities is human error, particularly failure in application of DP Operational procedures, it was urgent to act to improve safety, both for BOURBON vessels and for other assets in vicinity.
By employing smart technology, redefining bridge ergonomics and improving DP contingency procedures, the DP automation application, developed by BOURBON alongside partners Kongsberg Maritime and Bureau Veritas, continuously monitors a vast array of parameters, which are fed into the system by multiple sensors, to actively optimize adjustments to positioning and guiding operators in non-normal situations.
By introducing semi-autonomous technology, automation applications will result in safer and more effective operations.SHAM PARASRAMMARINE TEAM LEAD, BP TRINIDAD & TOBAGO LOGISTICS
A range of advantages
The increased level of automation will primarily result in improved safety, particularly within the 500-metre safety zone, but it also offers additional advantages. Namely, because the system regulates engines and propellers power output, feedback data provided by sensors may be used as input to predictive maintenance program, to improve operating efficiency. The optimized operation of the engines also means less maintenance and lower fuel consumption, a benefit that is appreciated by the customer.
A further advantage of the new system is particularly useful to the vessel’s crew in terms of manning. With the new system, apart from the captain, mate and specialized DP Officer, a fourth crew member will also be able to operate the system. Primarily a mechanic or electrician, this person will receive specific training allowing him to double as a junior DP operator.
The DP automation application is currently being tested on one of the company’s most modern vessels, the Bourbon Explorer 508, servicing a BP drilling platform in Trinidad. BP was motivated to take part in the pilot project, as Sham Parasram, Marine Team Lead in the Logistics department at BP Trinidad and Tobago, explains: “BP is in favour of increasing the use of semi-autonomous technology. It offers not only in greater efficiency but also and, most importantly, greater safety. By reducing the human factor, this automation application will reduce the risk of accidents. We are also expecting to see reduced diesel consumption, which will reduce our costs.”
The next stage of development
This application will be connected to an onshore control center, which will centralize data and enable a high level of real-time supervision. This will make it easier to pool data from the whole fleet to enhance the data available for decision-making on each vessel.
A drive for modernization
Thanks to the advent of the digital revolution, this type of remote monitoring is increasingly prevalent in all parts of the oil and gas industry – it mirrors a system called Well Advisor currently being rolled out by BP to monitor and supervise drilling and extraction operations, for instance. Its aim is to enable better decisions to be made.
BP also uses other digital applications to help increase operating efficiency. They have introduced an e-manifest which is a software used when cargo is loaded onto boats. Another new system, developed by BP’s Trinidad and Tobago logistics team, is an electronic version of the checklist that has to be completed before a vessel can enter the 500-metre zone. This can now be carried out rapidly on a tablet, avoiding the need for paper documents.
“BP is engaged on a drive for modernization,” remarks Sham Parasram. “As far as we are concerned, the more smart technology and advanced applications that can be used, the safer and more effective all our operations will be. By collaborating with BOURBON Offshore and its partners on the automation applications project, we are helping to transform the industry.”
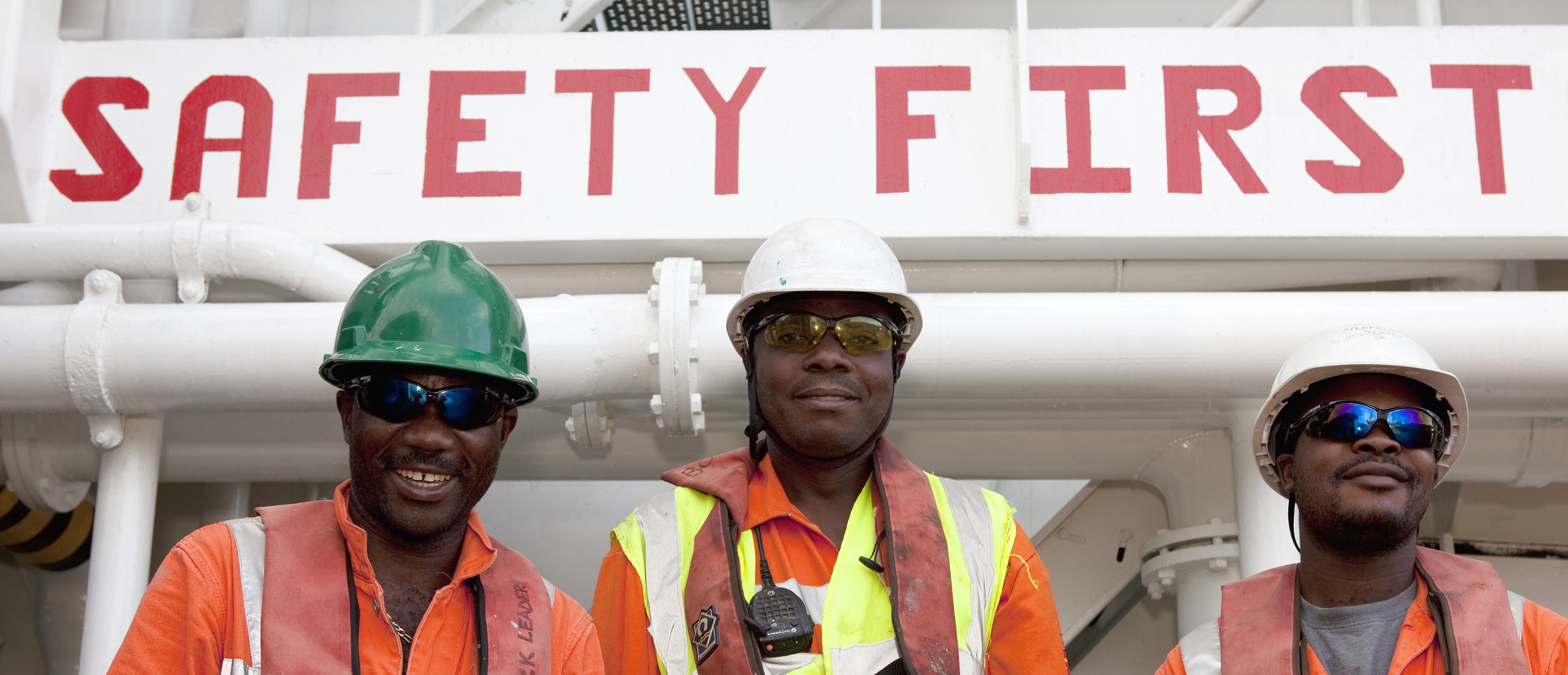
The golden rules: making safety a day-to-day reflex
In 2018, BOURBON is launching its “LIFE SAVING RULES”, a synthesis of the major safety rules that each employee must understand, share and apply, both aboard and onshore. An ideal occasion for Patrick Lievre, BOURBON’s Corporate HSE Manager, to exchange views with Jérôme Dupont, TOTAL’s Human and Organizational Factors of Safety Manager.
TOTAL possesses a set of Golden Rules for Safety at Work: what is their objective?
Jérôme Dupont: The 12 golden rules for safety at work that we have identified provide a common base of simple rules that apply to all our employees and contractors. A golden rule is a reflex to acquire, an ultimate rule to be applied in all circumstances and which should not be broken.
What about BOURBON’s Life Saving Rules?
Patrick Lièvre: The causes of our accidents are almost always identical. Despite the effectiveness of our “Safety Takes Me Home” campaign over the past few years, we have observed that BOURBON does not have a set of easily identifiable and memorizable safety rules that correspond to these accidents. That is why we have decided to provide our employees with these easily accessible “Life Saving Rules”. They are a synthesis of rules that already exist in the company expressed in the form of Do’s and Don’ts, similar to what TOTAL has done, in fact.
12 rules
which should enable us to avoid 80% of our incidents and 100% of fatal accidents
How were they established?
P.L.: Our “Life Saving Rules” were officially distributed within the group at the beginning of 2018. They are based on an analysis of our own incidents and on a study of the rules in force among our peers.
J.D.: In our case, it was after 2009, a year that was difficult for us in terms of safety, that we felt the need to return to a limited number of simple safety rules applying to the sectors with the highest number of accidents. We therefore carried out an accidentology study and defined 12 rules expressed in the form of obligations and prohibitions. When correctly applied, they should enable us to avoid 80% of our incidents and 100% of fatal accidents.
How do they fit into your overall safety policy?
P.L.: The Life Saving Rules fall in line with our standards, like the OSM (Operational Safety Management), our existing safety campaigns, and our “Stop Work Policy” for use in the event of non-compliance with procedures. Our goal is to involve each of our employees and to encourage them to facilitate reporting in the case of danger and to legitimize interventions.
J.D.: At TOTAL, conversely, the “Stop Card”, which gives the holder the authority to intervene at any time if a situation seems dangerous, appeared after the golden rules. We encourage our employees and contractors to show zero tolerance and to systematically use the “Stop Card” whenever a breach of the rules is observed.
A golden rule is a reflex to acquire, an ultimate rule to be applied in all circumstances and which should not be brokenJérôme DupontTOTAL’s Human and Organizational Factors of Safety Manager
How have these rules been implemented?
J.D.: We have multiplied the tools and actions to anchor these golden rules into day-to-day safety with displays, e-learning, booklets dedicated to specific rules, and an annual campaign covering several specific rules. All operators, whether they are TOTAL employees or not, are trained for the golden rules and their knowledge is tested.
P.L.: It is the same for BOURBON. The “Life Saving Rules” campaign is supported by communication via our in-house tools, but also through on-site posters and flyers. Information cascading is a real challenge for a company like ours and we are doing everything to ensure the fast and efficient deployment of our “Life Saving Rules”. No seagoing or shore-based employee should ignore them.
J.D.: I would add that the World Day for Safety on April 28 always provides an opportunity to organize competitions and initiatives based on the golden rules to facilitate their adoption.
P.L.: Absolutely. We also take advantage of this very special day to focus messages on the importance of the culture of safety within the group. Our “Life Saving Rules” will be very widely promoted by our teams in 2018.
Do you think that a set of standardized golden rules should be established for the entire sector?
J.D.: It is a very pertinent question, but the problem is one of managing change. All stakeholders globally agree on the principal. Nevertheless, I am convinced that the definition of rules specific to each company contributes to their adoption, even if it can complicate things for our contractors.
P.L.: I agree entirely. A specific terminology for each stakeholder is essential to facilitate the adoption of these rules by employees.
The final word: How do you see the establishment of these rules by BOURBON?
“We encourage this initiative 100% and are ready to exchange ideas with BOURBON in order to progress. With hindsight, our first formulation of the golden rules was probably too complex, so our recommendation is to be as simple as possible. Another piece of advice: repeat your communications, renew the messages to guarantee their sustainability, and ensure that they become part of your company’s DNA.”
Jérôme Dupont
TOTAL’s Human and Organizational Factors of Safety Manager
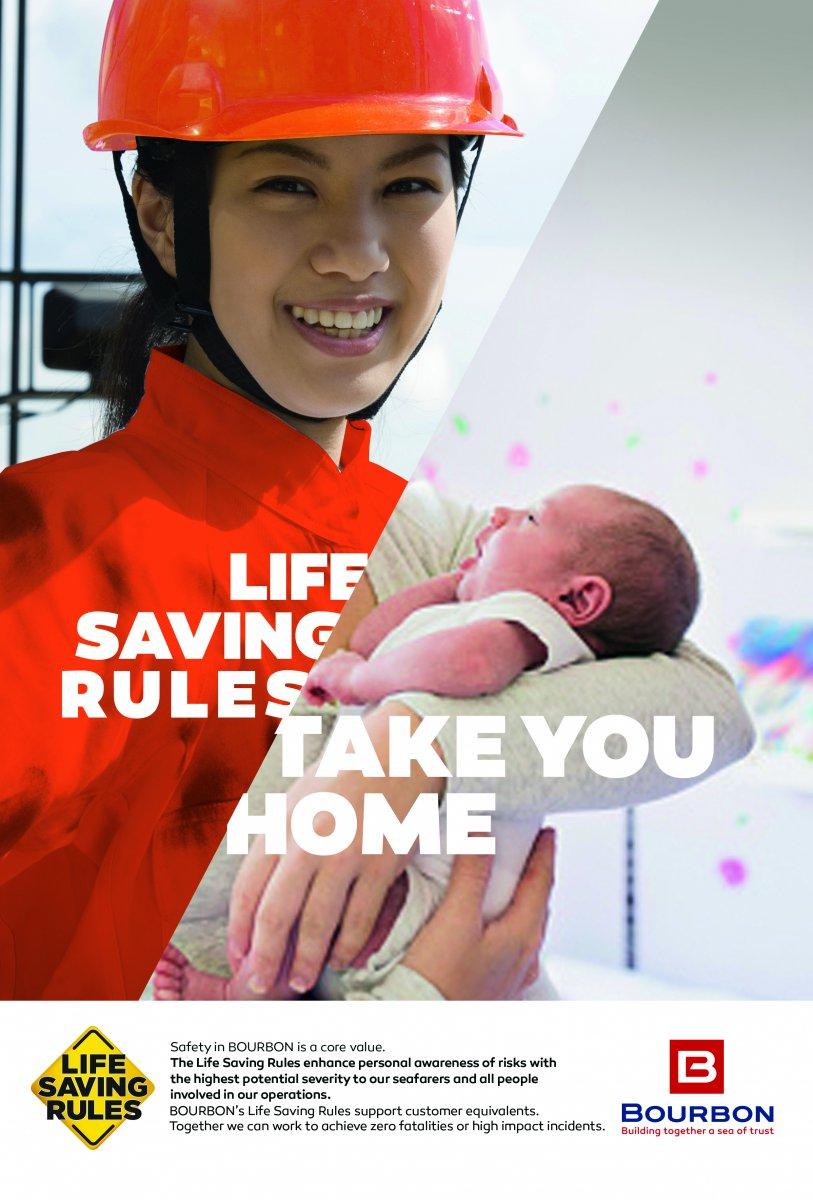
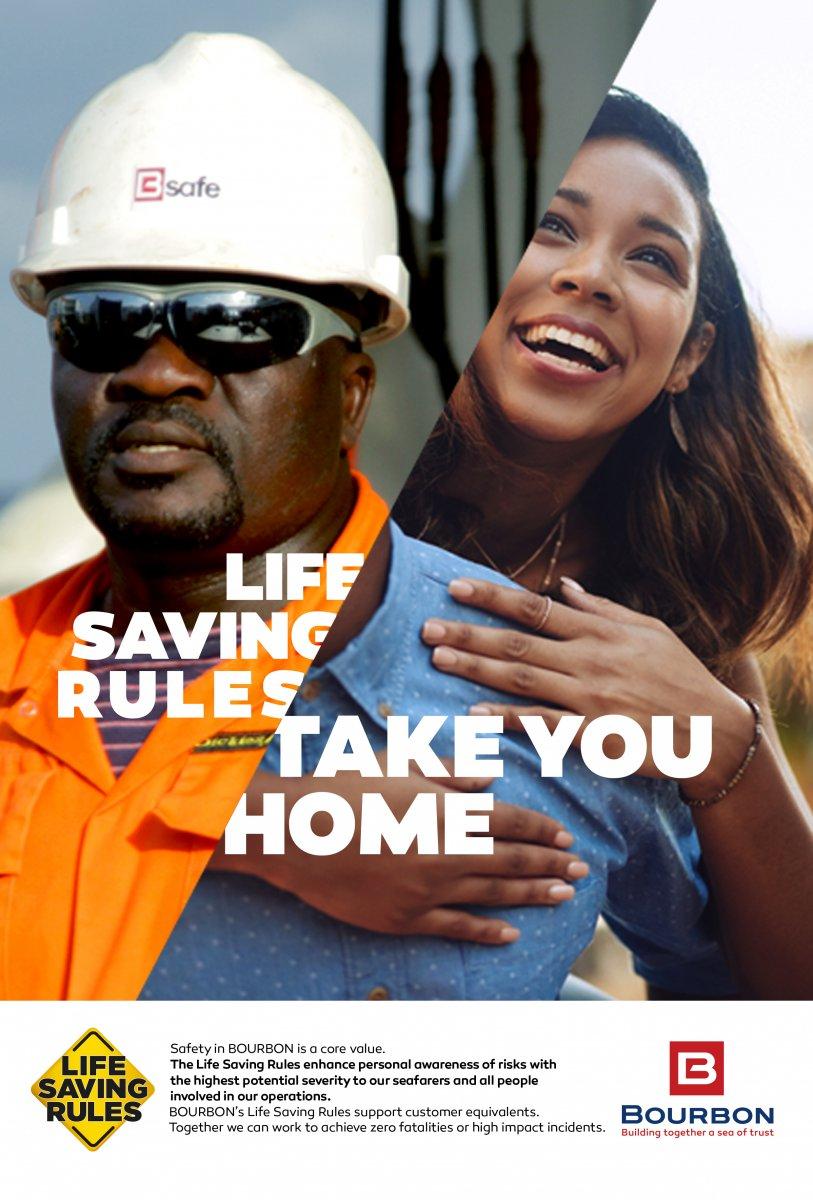
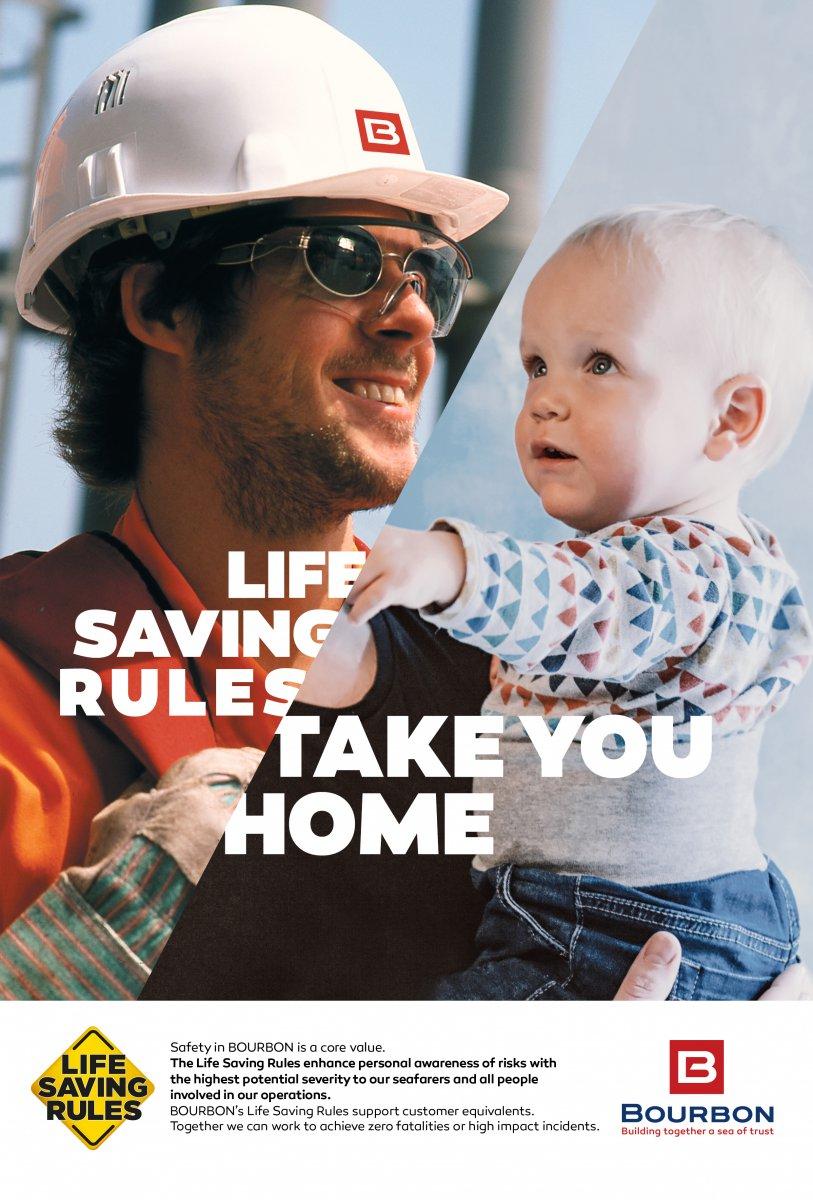
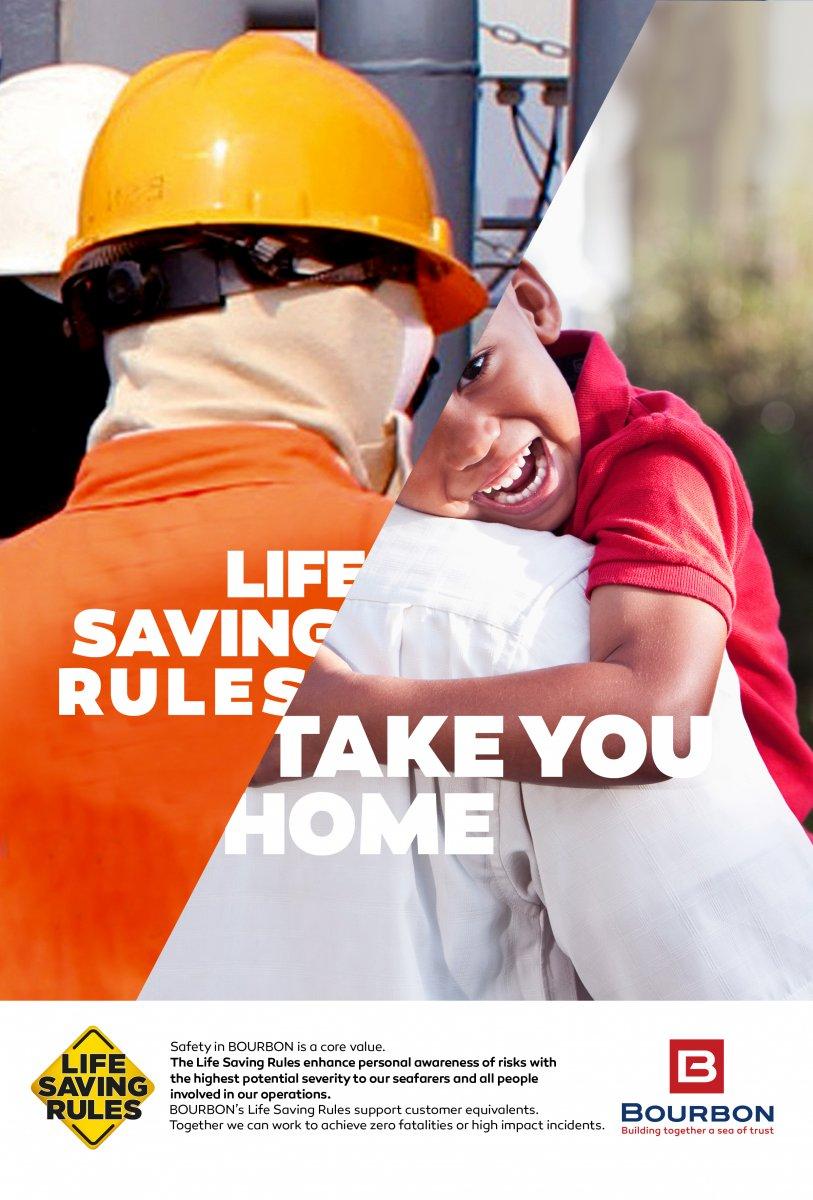
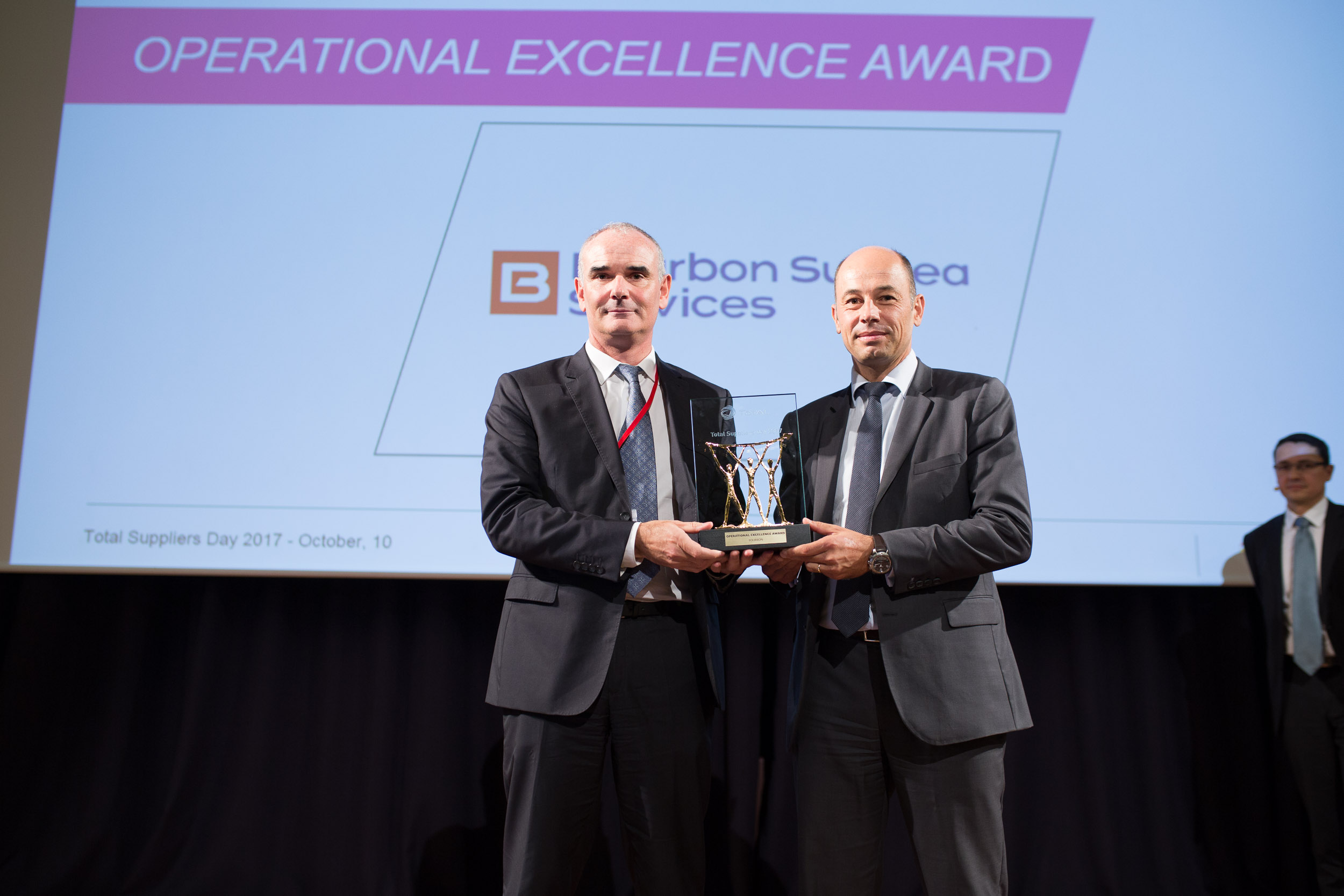
Well restarting: TOTAL awards BOURBON with its prize for operational excellence
During its traditional Suppliers’ Day last October, TOTAL awarded BOURBON with the prize for the operational excellence for the “well clean-up” or well restarting operation carried out from a vessel, Bourbon Evolution 801. A success that demonstrates BOURBON’s agility and its ability to listen to its clients to offer them services that are adapted to their needs.
Well clean-up operations are usually carried out from a mobile platform or jackup rig. However, last January, the well restarting operation at TOTAL’s OFON field in Nigeria was carried out from an MPSV (Multi-Purpose Support Vessel), Bourbon Evolution 801. The objective: to work faster, safely, and at a lower cost. For this operation, the vessel was fitted out with hydrocarbon separators, additional storage capacity, and 2 lines for hydrocarbon import and gas export/return towards the platform. Before starting the operation, both partners studied the situations in normal and degraded mode, as well as the decision-making process to handle any incidents. Trial exercises were also carried out by the captain, his crew, and the TOTAL team in order to acquire the right reflexes for the operation.
The anticipation and analysis of safety risks were capital for the success of this operation.
“The captain must be in a position to rapidly make the right decision in the event of a well blowout or gas freeing via the oilfield flare. The recuperation of hydrocarbons aboard the vessel is a special operation that is risky and demanding. Each step must be perfectly controlled...”, highlights Patrick Belenfant, Senior VP Subsea Services.
Anticipate, analyze, adapt
This innovation was recognized by the award of TOTAL’s operational excellence prize during its “2017 Suppliers’ Day”. This award commends the quality of execution and the safety of this operation, but also the cost reductions it provided, with 4 million dollars of savings for the company. Not to mention the fact that the duration of the operation was reduced to 30 hours! Beyond these tangible results, this recognition distinguishes BOURBON’s capacity to adapt itself to offer innovative solutions that are adapted to its clients’ expectations. “Our close ties with TOTAL, our long-standing cooperation, and the skills and professionalism of our crews enabled us to succeed.”
A demonstration of reliability
“We hope that this well clean-up will open the way for similar operations in the future”, concludes Patrick Belenfant. “Knowing that we have carried out this operation for TOTAL is a demonstration of our reliability for our other clients.”
“Rather than calling on a platform or a drill ship, TOTAL preferred to innovate and perform this operation from one of our vessels. We worked in collaboration with TOTAL to analyze the pollution and safety risks in order to implement all the mitigation measures necessary for the proper conduct of this operation.”
Hélène Butat, Project Manager
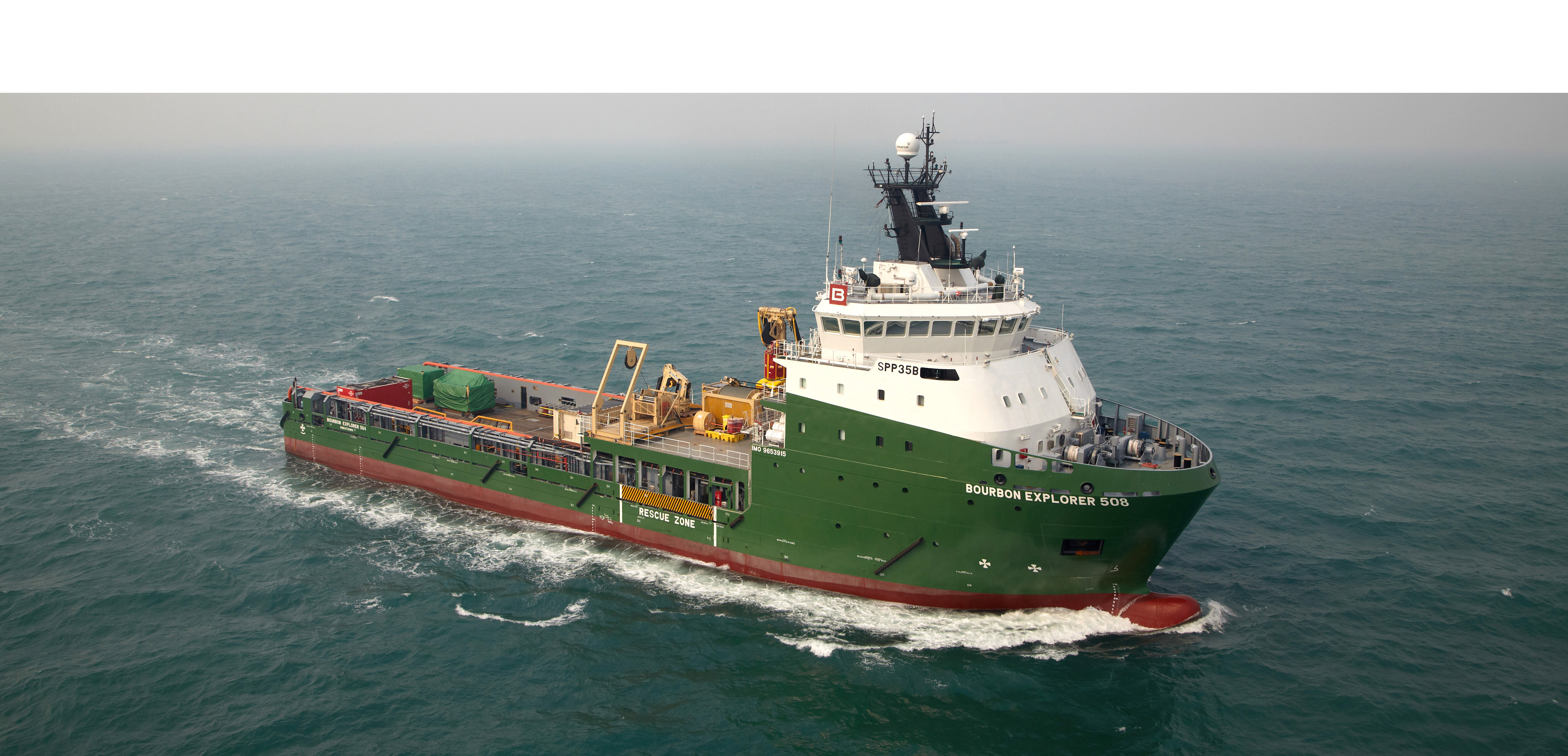
BOURBON – Bureau Veritas partnership: reliable operations at optimized costs
BOURBON and Bureau Veritas (BV) have formed a strategic partnership to digitize vessels operations. Let's talk about the collaboration with Jean-François Segretain, Technical Director, Marine & Offshore, Bureau Veritas, and Frédéric Moulin, Operational Standards & Innovation Vice President at BOURBON.
What led to this collaboration?
Jean-François Segretain: It’s part of our DNA at Bureau Veritas to support our clients to ensure safety and security when they install new technologies on their vessels. Smart vessels technologies offer shipowners an opportunity to achieve better performance, to reduce costs and to operate more sustainably. Bureau Veritas has carried out an internal digital transformation, and we have invested in skills and tools specific to Smartships. We now need to test our new approach with clients to ensure that we have correctly understood their needs. Having classified a large number of BOURBON vessels, we have worked very closely together over the years, so understand the BOURBON business, and were very keen to collaborate to continue to develop our smart vessels offering.
Frédéric Moulin: It’s the first time we’ve collaborated on the topical area of digital technologies, but we have worked together a lot in the past on maritime specifications. Opportunity to collaborate on this topic came from mutual willingness to develop and deploy concrete smart shipping principles.
The fact that the innovations are certified proves that they comply with classification specification.
What are you aiming to achieve from the partnership?
F.M.: Smart shipping means reducing operating costs while maintaining the highest standards of quality and safety. Using digital technology and modernizing some of our vessels will make us more efficient and productive, but we have to convince our clients that we mitigate operational risks caused by the change – oil and gas sector players have a very strong safety culture. So it’s important to us that they accept the innovations we are introducing. This is why our partnership with Bureau Veritas is essential. Our clients know we have assessed all the risks concerning safety, pollution, etc., with a player perfectly familiar with all the regulations.
J.-F.S.: The fact that that the innovations are certified proves that they comply with classification specifications. To be able to provide such certificates, the partnership allows BV to be involved upfront in BOURBON projects and to support BOURBON to make sure risks are properly identified and mitigated.
F.M.: Our joint work focuses on new technologies with which certain tasks can be automated or streamlined while respecting all the regulations.
A pilot system of advanced automation of dynamic positioning has already been developed and implemented on the Bourbon Explorer 508, operating in Trinidad. What role has Bureau Veritas played?
J.-F.S.: 18 months ago BOURBON asked us to perform a risk analysis of a project to automate navigations systems and reorganise the vessel bridge. We later reviewed the design planned for these new systems and organizations, and went on board the vessel to verify that the equipment was correctly installed. At the same time, we knew that the transmission of data to land would create new cyber-security risks. We carried out the same process of assessing the risks upstream and then certifying that they had been managed as required by BV classification rules.
We are digitizing our inspection processes at Bureau Veritas, and there are technologies that have already been validated by the regulatory authorities that we are sharing with BOURBON to save time.Jean-François SegretainTechnical Director, Marine & Offshore, Bureau Veritas
What is the next phase of the partnership?
F.M.: We are at the innovation stages of looking at further opportunities to connect and modernise the bridge as part of our Smart shipping program, including digitalizing all the workstations with more autonomous and intelligent Dynamic Positioning software. We will be working with Bureau Veritas on remote supervision systems and on Smart Apps for the crew, developing what we believe will become the new standards.
J.-F.S.: BOURBON is working with the equipment supplier Kongsberg Maritime, developing a continuous verification of the DP system and at Bureau Veritas we are working on procedures to enable continuous verification to reduce the need for DP inspections. The benefit for us both is that we are doing concrete work in helping to develop a pilot. Working on this project is giving us, as well as BOURBON, an edge.
Our clients know we have assessed all the risks concerning safety, pollution, etc., with a player perfectly familiar with all the regulations.Frédéric MoulinVice President, Operational Standards &, Innovation, BOURBON
Bureau Veritas, a world leader in maritime certification
Bureau Veritas is one of the world’s leading players in conformity assessment and certification, helping its clients meet the growing challenges of quality, safety, environmental protection and social responsibility. Active in a wide range of industries and sectors, one of its specialist divisions covers Marine and Offshore Industries. Bureau Veritas classifies vessels and carries out inspections, helping shipowners to implement the latest legislation covering safety, security and maintenance. It is committed to developing the use of digital technology to improve its clients’ operational performance.